TECHNICAL INFO
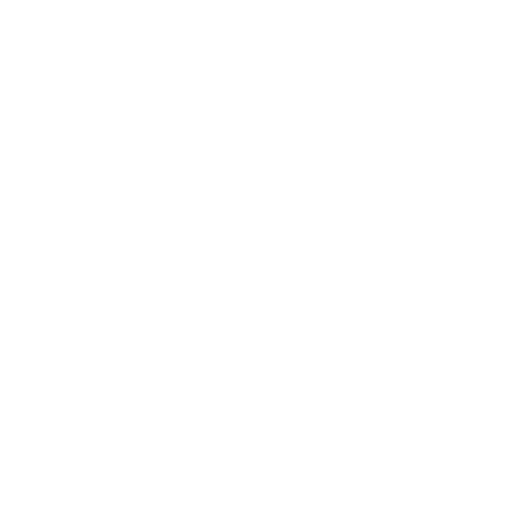
TECHNOLOGY
END MILL technical info
- Definition of end mill
- Things to consider
when using an end mill - Issues and solutions when
using an end mill - Conditions of use of end mill
- Definition of end mill
- Things to consider whenusing an end mill
- Issues and solutions when using an end mill
- Conditions of use of end mill
What is
an end mill?
It is defined as a shank type milling cutter that has a cutting edge on the outer surface and cross-section. An end mill is a tool that rotates and shaves the sides and top surface of a processed item with an outer blade and a bottom blade of a cross-section, respectively. End mills are especially used in precision processing of electrical, electronic and automotive parts and molds.
Selection
of end mill
The performance of an end mill varies depending on the settings such as the number of blades, twist angle, inclination angle, relief angle and coating type, and a suitable shape is required for high-speed cutting operations.
The main part
details of End mills
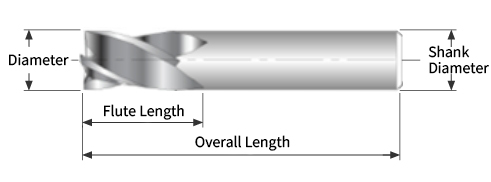
|
Maximum outer diameter of end mill cutting edge |
|
Maximum outer diameter of end mill shank |
|
Endmill cutting edge length |
|
Distance from end mill blade tip to shank tip |
Side Blade
Related Names
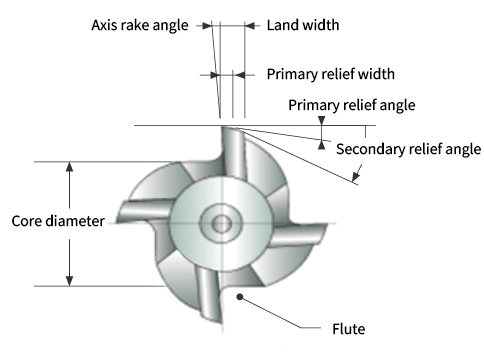
This is the angle between the concave tip of the side cutting edge and the imaginary axis of centerline when looking directly at the base of the end mill, and is a critical factor in the cutting performance of the end mill.
The primary angle of the endmill’s side cutting land, which, like the axis rake angle, is critical to cutting performance.
This is the angle after the primary relief angle and ensures that there is sufficient clearance between the workpiece and the end mill when cutting.
The overall width of primary and secondary margins.
The flute is used as a passageway for chips to pass through when cutting, and if the flute becomes smaller, chip evacuation will not be smooth, affecting the roughness of the cutting surface.
Bottom blade
related names
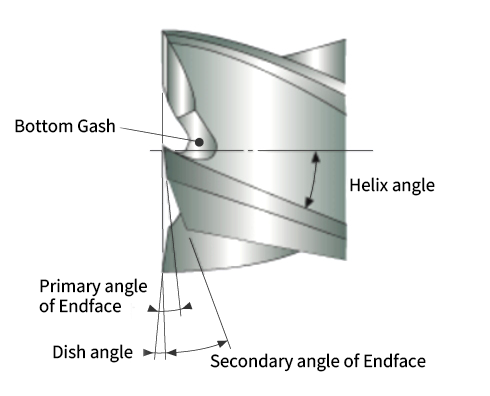
The angle that a twisted side cutting blade makes with respect to an arbitrary axis line.
The endface teeth attached to the bottom of the cylindrical end mill.
An outlet for the processed chips to improve the flow of chips out during cutting.
The angle at which the endface teeth is inclined to the axis line.
The angle at which the endface’s primary land is inclined to the axis
The angle at which the endface’s secondary land is inclined to the axis line.
An arbitrary imaginary line passing through both ends of the endface’s cutting edge and the angle that the cutting edge makes with the center of the diameter.
Product shape
depending on the number of blades
The performance of an end mill varies depending on the settings such as the number of blades, twist angle, inclination angle, relief angle and coating type, and a suitable shape is required for high-speed cutting operations.
The rigidity of tools
by the length(L) of the flute

The shorter length of tools, the higher the rigidity and performance of cutting. The length of the flute become twice, the rigidity of end mills falls to 1/8. Because end mills are the tools to move horizontal, it is important for the rigidity of tools to be in inverse proportion to the length of tools. Using a longer flute that need be is not good. You can choose suitable flutes for your cutting conditions now that COGO TOOLS, we have a variety of items.
Helix angle
|
Used for applications that require precision in processed width and inclination |
|
Used for typical processing |
|
Primarily used for side cutting thanks to its outstanding machinability, and also used on light allows such as aluminum and difficult to cut processing |
Issues and solutions when using an end mill
Problem | Cause | Solution |
---|---|---|
Damaged blades |
|
|
Vibration occurred during cutting |
|
|
Reduced cutting performance |
|
|
Sudden occurrence of wear |
|
|
Poor chip discharge |
|
|
Poor surface roughness |
|
|
Damaged during cutting |
|
|
Poor processed dimensions |
|
|
Conditions of use of end mill
Number of blades
This is one of the most essential factors that determine an end mill’s performance. If the number of flutes on an end mill are small,
it would result in a small cross-sectional area and, thus, reduce stiffness, which may cause bending during cutting.But, on the other hand there is a large space for extract of chips, which makes the extract the chips better. If the number of flutes are large, the chip pocket becomes small to allow a reduced capacity for chip storage but, conversely, its cross-sectional area as well as stiffness increase.
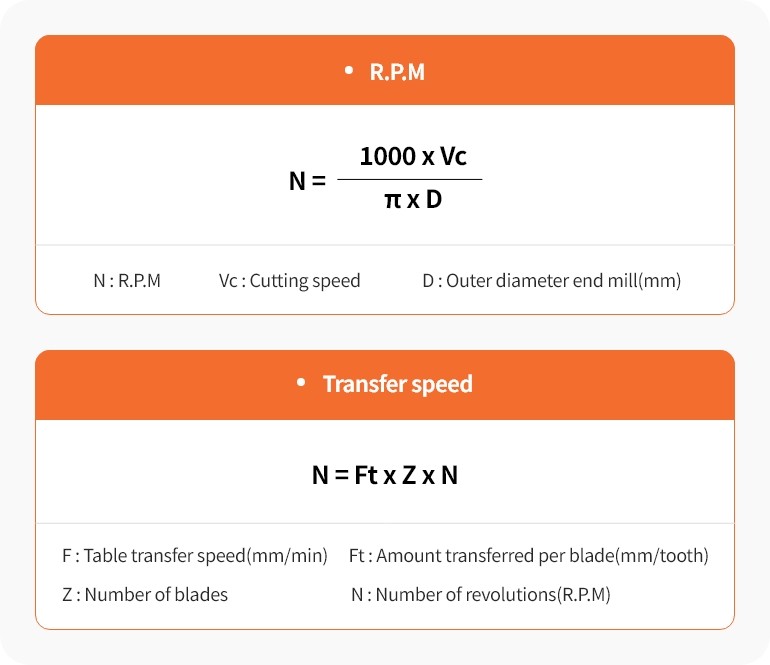
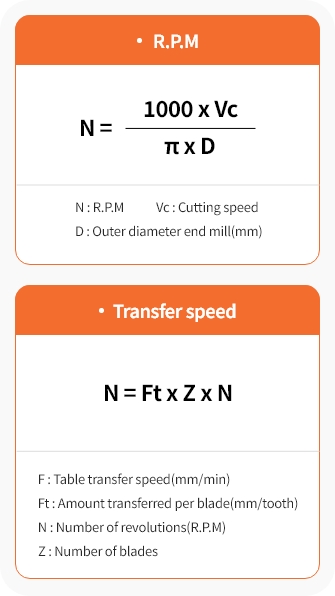